Why Are Welding Symbols Used? Representation!
Welding symbols act as a universal language, ensuring you can communicate effectively in your projects.
They standardize specifications across diverse teams, detailing the type, dimensions, and requirements of welds with precision. This clarity reduces project time and construction errors, enhancing efficiency and safety.
By accurately conveying weld requirements, they maintain structural integrity, streamline international collaboration, and facilitate quality assurance.
Symbols bridge the gap between engineering concepts and physical fabrication, minimizing misunderstandings and promoting safety.
As you grasp the significance of these symbols, you’ll appreciate their role in accident prevention and project success. Unlocking their full potential takes your skills further.
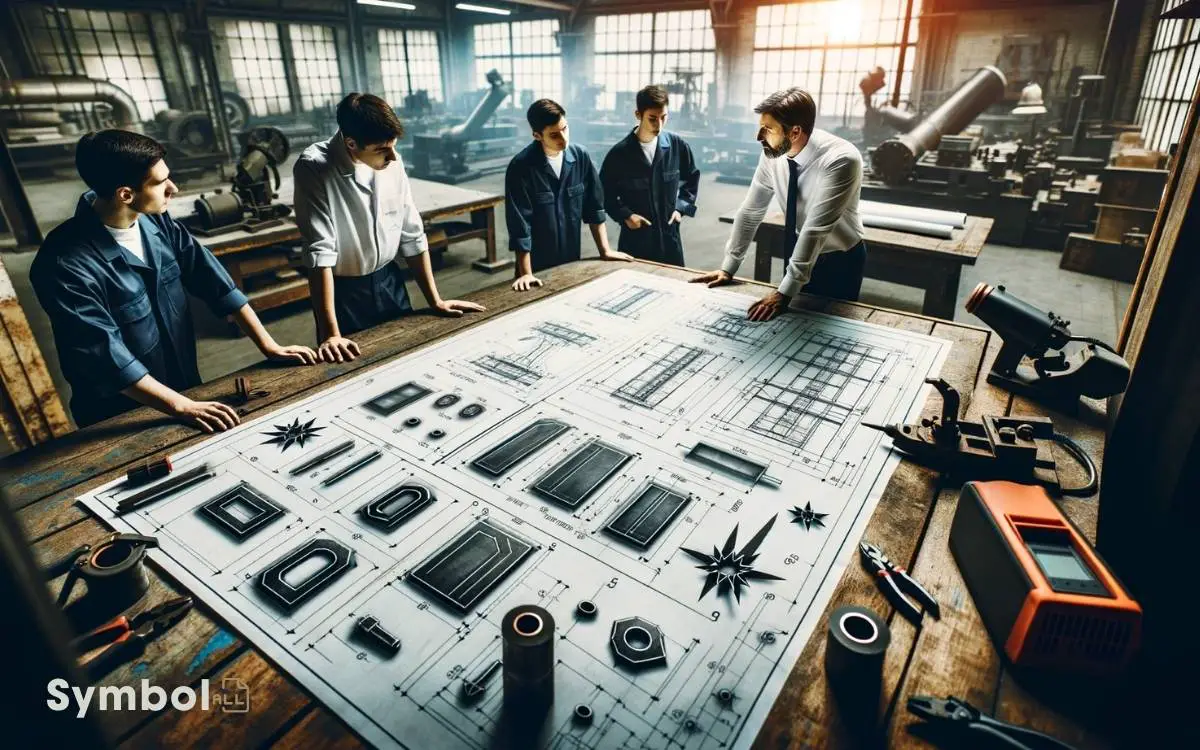
Key Takeaways
Standardizing Communication
In the realm of industrial fabrication, standardizing communication through welding symbols ensures that all stakeholders are on the same page, minimizing errors and enhancing efficiency.
These symbols serve as a universal language, bridging gaps between diverse teams who may speak different languages or have varying levels of expertise.
You’ll find that each symbol precisely conveys the type of weld, dimensions, and other critical specifications required for the project at hand.
This clarity eliminates guesswork, ensuring that welders and supervisors understand exactly what’s needed without extensive verbal explanations.
To master this language, you’ll delve into detailed diagrams and specific notation systems, studying the nuances of each symbol.
This knowledge empowers you to interpret and communicate welding requirements accurately, fostering a seamless workflow from blueprint to final weld.
Enhancing Project Efficiency
How does the implementation of standardized welding symbols contribute to enhancing project efficiency?
When you’re working on a welding project, time is often of the essence. Standardized welding symbols streamline communication among team members, allowing for swift interpretation and action.
These symbols serve as a universal language, eliminating the need for lengthy explanations or clarifications that can slow down project momentum.
By leveraging these standardized notations, you’re able to reduce the time spent on project planning and revisions. You’ll find that this leads to a more seamless workflow, where tasks are executed more quickly and efficiently.
Consequently, projects can be completed within shorter timelines, optimizing resource allocation and ultimately enhancing overall project efficiency.
This precise approach ensures that every team member is on the same page, fostering a more cohesive and productive working environment.
Reducing Construction Errors
Standardized welding symbols significantly reduce construction errors by ensuring clear, unambiguous communication across the project team. These symbols serve as a universal language, conveying complex welding requirements with precision.
By adhering to a standardized set of symbols, you eliminate misunderstandings that could lead to costly and potentially dangerous construction errors.
Symbol Type | Meaning | Application |
---|---|---|
Fillet | Triangle shape indicates fillet weld | Joins two surfaces |
Groove | Rectangle shape for groove weld | Edges preparation |
Square | Square end indicates square weld | Butt joints |
Understanding these symbols allows you to accurately interpret the welds required, ensuring the structural integrity and safety of the construction project.
This precision is crucial in minimizing errors, fostering a streamlined construction process free from costly rework or modifications.
Ensuring Design Accuracy
Understanding welding symbols not only minimizes construction errors but also ensures the accuracy of the design by clearly conveying specific welding requirements. These symbols serve as a universal language that enables you to grasp intricate details without ambiguity.
Here’s how they contribute to design precision:
- Detailing Specific Joint Types: They specify the exact type of joint needed, be it butt, corner, lap, or edge.
- Indicating Weld Dimensions: Symbols provide critical dimensions, including length, depth, and angle, ensuring welds meet structural requirements.
- Highlighting Welding Processes: Certain symbols suggest the most suitable welding process, guiding you in choosing between TIG, MIG, or stick welding.
- Specifying Additional Treatments: They can dictate necessary post-weld treatments such as grinding or heat treatment, crucial for achieving the desired finish and structural integrity.
Facilitating International Collaboration
You’ll find that welding symbols play a crucial role in bridging language barriers across global teams, ensuring everyone’s on the same page regardless of their native language.
They also standardize design interpretations, mitigating the risk of costly misunderstandings in complex projects.
Furthermore, these symbols significantly enhance project efficiency by streamlining communication and reducing the need for lengthy explanations.
Bridging Language Barriers
Welding symbols serve as a universal language, effectively bridging communication gaps between international teams in the fabrication industry.
You’ll find that these symbols allow for:
- Precision in Instructions: Ensuring that every detail of the welding process is understood, regardless of the welder’s native language.
- Efficiency in Workflow: By eliminating the need for lengthy explanations, projects move forward faster.
- Consistency Across Borders: Guaranteeing that the same standards are applied worldwide, maintaining the integrity of the design.
- Ease of Training: Facilitating the learning process for welders globally, as they only need to master one set of symbols.
This standardization not only enhances collaboration but also ensures that every team member, irrespective of their background, contributes effectively to the project.
Standardizing Design Interpretations
By standardizing welding symbols, teams across the globe can interpret design plans consistently, ensuring seamless international collaboration.
This standardization process aligns with universally accepted codes, such as those established by the American Welding Society (AWS) or the International Organization for Standardization (ISO).
These guidelines dictate the shape, dimension, and type of welds, providing a common language for engineers, fabricators, and welders worldwide.
Such a unified approach eliminates ambiguity, enabling you to understand the specific requirements of a joint or weld without direct verbal communication.
It ensures that regardless of geographical location, you’re equipped with the knowledge to accurately execute or review a welding task, adhering to the intended structural integrity and design specifications.
This standardization is pivotal in maintaining design integrity across international projects.
Enhancing Project Efficiency
Adopting standardized welding symbols significantly boosts project efficiency, particularly in fostering smoother international collaboration.
When you’re part of a project that spans across borders, understanding and utilizing these symbols can streamline communications and reduce errors.
- Universal Language: Creates a common language, minimizing misunderstandings due to language barriers.
- Error Reduction: Precise symbols limit interpretation errors, ensuring everyone’s on the same page.
- Training Efficiency: Simplifies training processes, as workers globally learn the same symbols.
- Quality Assurance: Standardization supports consistent quality checks, vital for projects requiring uniform standards across different countries.
Simplifying Complex Instructions
To ensure accuracy and efficiency in interpreting fabrication instructions, welding symbols simplify complex designs into universally understandable diagrams.
These symbols serve as the language of the welder, translating intricate engineering plans into clear, actionable steps.
You’ll find that each symbol encapsulates specific details from the type of weld needed to its size, length, and even the precise location on the workpiece.
This system eliminates the ambiguity that often accompanies verbal or written descriptions, ensuring you’re working with concrete, error-minimized guidance.
Supporting Quality Assurance
Welding symbols play a critical role in supporting quality assurance across your projects. They ensure consistent standards are met, making it easier for you to facilitate inspection processes efficiently.
Moreover, these symbols are pivotal in promoting safety compliance, safeguarding both workers and the final structure.
Ensuring Consistent Standards
Ensuring consistent standards across all welding projects supports quality assurance by providing a clear, universally understood language through symbols. This approach is critical for maintaining the integrity and safety of welded structures.
Here’s how it’s done:
- Uniformity: Welding symbols standardize designs, ensuring every welder interprets the requirements uniformly, regardless of geographic location.
- Precision: These symbols convey exact specifications, such as dimensions and welding techniques, reducing the margin for error.
- Efficiency: A standardized symbol set speeds up the communication process between designers and welders, minimizing delays.
- Adaptability: The system is robust, accommodating a wide range of welding processes and materials, ensuring consistent quality across diverse projects.
This methodology guarantees that welding quality is never compromised, fostering trust in the construction and manufacturing industries.
Facilitating Inspection Processes
Building on the foundation of consistent standards, the use of welding symbols significantly streamlines the inspection process, reinforcing the commitment to quality assurance.
These symbols serve as a universal language, ensuring that every detail of the welding task, from the type of weld to its dimensions, is communicated clearly and efficiently.
This precision aids inspectors in verifying that welds meet the stringent criteria set forth in the design specifications, thereby supporting the overarching goal of quality assurance.
Symbol | Meaning |
---|---|
\ | Groove Weld |
= | Fillet Weld |
O | Spot or Projection Weld |
– | Seam Weld |
U | J-groove Weld |
Each symbol embodies specific instructions for the welding process, which inspectors use to assess compliance with design requirements, bolstering both the reliability and integrity of the welded structure.
Promoting Safety Compliance
Beyond enhancing quality assurance, integrating welding symbols into project designs also plays a crucial role in promoting safety compliance.
These symbols are pivotal in ensuring that welding operations adhere to stringent safety standards, thereby minimizing risk and safeguarding the wellbeing of everyone involved.
Here’s how:
- Clarifying Specifications: They provide clear, unambiguous specifications for welds, reducing the risk of incorrect execution that might compromise structural integrity.
- Standardizing Procedures: Promote the use of standardized welding procedures, ensuring consistent application of safety practices.
- Facilitating Communication: Serve as a universal language, improving communication among diverse teams, which is essential for maintaining a safe working environment.
- Aiding in Risk Assessment: Help in identifying potential risks in the welding process, allowing for the implementation of preventive measures.
Streamlining Project Management
Incorporating welding symbols into project designs significantly streamlines project management by facilitating clear, concise communication across teams.
These symbols serve as a universal language, ensuring that project specifications are understood precisely, regardless of individual backgrounds or experiences.
This clarity reduces the risk of errors and misunderstandings, leading to a smoother workflow and more efficient use of resources.
By standardizing the way welding requirements are communicated, project managers can easily verify compliance with design specifications, monitor progress, and make adjustments as needed without extensive verbal explanations or revisions.
Furthermore, this standardization supports effective planning and allocation of tasks, enabling teams to work in a more coordinated and efficient manner. Ultimately, the use of welding symbols contributes to the timely and cost-effective completion of projects.
Bridging Engineering and Fabrication
Welding symbols not only streamline project management but also serve as a critical bridge between engineering designs and the actual fabrication process. They ensure that the intricate details of the engineering plans are accurately translated into physical structures.
- Standardization: Welding symbols follow a standardized system understood globally, ensuring that designs are interpreted correctly regardless of the fabrication team’s location.
- Precision: They convey specific instructions, such as weld type, size, and length, minimizing errors in fabrication.
- Efficiency: Symbols enable quicker interpretation of designs, speeding up the fabrication process.
- Quality Control: By providing clear, detailed instructions, welding symbols help maintain the integrity of the final product, ensuring it meets the required specifications and standards.
Promoting Safety and Compliance
You’ll find that welding symbols play a crucial role in ensuring worker protection by clearly communicating specific safety requirements on technical drawings.
By adhering to these symbols, you’re not only meeting industry standards but also minimizing the risk of workplace accidents.
This precision in communication is key to maintaining a safe and compliant welding environment.
Ensuring Worker Protection
Understanding welding symbols is crucial for ensuring workers’ safety and compliance with industry standards. These symbols serve as a comprehensive language that communicates crucial details about the welding process.
By mastering this language, you’re not only enhancing the quality of your work but also significantly reducing the risk of accidents and ensuring a safer workplace.
- Identify Hazardous Materials: Symbols can indicate the use of materials that require special handling.
- Specify Protective Gear: Certain symbols dictate the need for specific safety equipment.
- Highlight Critical Weld Parameters: Understanding symbols helps in adhering to parameters that ensure structural integrity, reducing the risk of failures.
- Facilitate Clear Communication: Eliminates misunderstandings that could lead to hazardous situations.
Meeting Industry Standards
Mastering welding symbols not only enhances workplace safety but also aligns with industry standards, ensuring compliance and promoting a culture of accountability.
You’ll find that adhering to these symbols is crucial for meeting the regulatory requirements set forth by authoritative bodies. This adherence is not just a procedural formality but a commitment to excellence and safety in the welding industry.
Standard | Symbol Complexity | Compliance Impact |
---|---|---|
ISO 2553 | High | Mandatory |
AWS A2.4 | Moderate | Essential |
EN 22553 | Varied | Critical |
ASME IX | Detailed | Required |
JIS Z 3121 | Simplified | Advisable |
Understanding and applying these symbols precisely ensures your work not only meets the technical specifications but also upholds the highest safety standards, avoiding any compromises in quality or safety.
Preventing Workplace Accidents
Adhering strictly to welding symbols significantly reduces the risk of workplace accidents, ensuring both safety and compliance in the welding process.
These symbols serve as a universal language among professionals, guiding the execution of welding tasks with precision.
When you understand and apply these symbols correctly, you’re not just following a blueprint; you’re actively participating in a safety protocol that’s designed to prevent accidents before they happen.
Here are the ways in which welding symbols promote safety:
- Clarifying Joint Design: They specify the type of weld, dimensions, and exact location, reducing misunderstandings.
- Specifying Welding Processes: Certain symbols suggest the best technique to use, minimizing errors.
- Detailing Inspection Criteria: This ensures that welds meet safety standards before project completion.
- Highlighting Safety Requirements: Symbols can denote specific precautions, such as the need for ventilation or protective barriers.
Conclusion
In the intricate dance of construction, welding symbols are the unspoken language, synchronizing every step. They streamline communication, ensuring each weld is a stroke of precision on the canvas of engineering.
By reducing errors and enhancing efficiency, they’re the silent guardians of quality and safety, bridging the gap between design dreams and structural reality.
Embracing these symbols not only elevates project management but also fosters global collaboration, making them indispensable tools in the architect’s and fabricator’s toolkit.