Kanban Means Symbol or Box in Japanese
Kanban, derived from the Japanese term for "signboard" or "visual card," was developed by Taiichi Ohno at Toyota in the early 1940s. This methodology was essential in lean manufacturing to align production with actual demand and reduce waste.
Kanban uses visual cues like color-coded task cards and workflow status indicators to optimize efficiency, transparency, and continuous improvement. Implementing a Kanban system with visible workflow stages and work-in-progress limits enhances team collaboration and productivity.
Originating in automotive manufacturing, Kanban has since been successfully adopted across various industries worldwide. For a deeper understanding of its principles and applications, further exploration is encouraged.
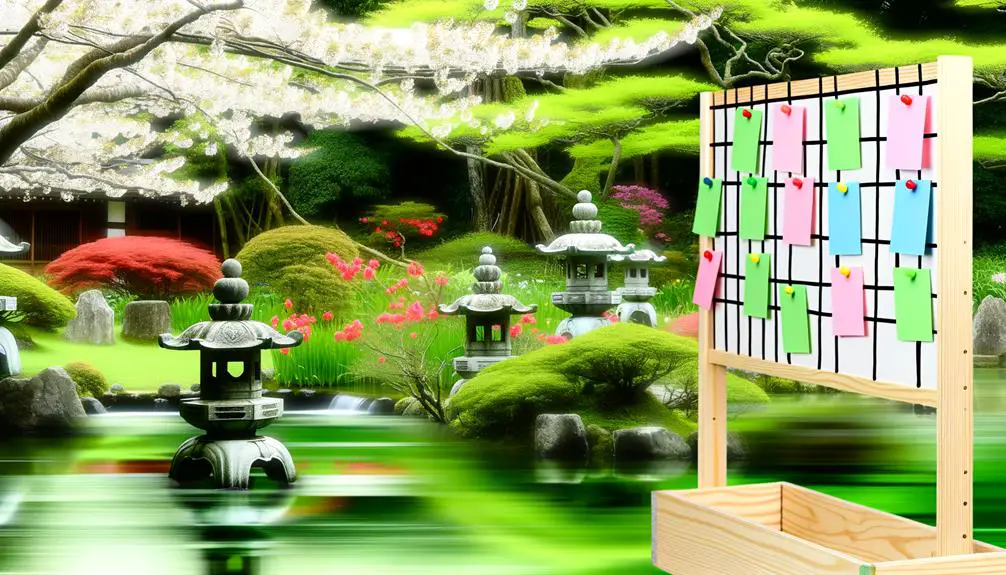
Key Takeaways
- Kanban is a Japanese term meaning 'signboard' or 'visual card.'
- Developed by Taiichi Ohno at Toyota in the 1940s.
- Originated as a method to align production with demand.
- Utilizes visual cues like color-coded cards for workflow management.
- Aims to reduce waste and enhance process efficiency.
Origins of Kanban
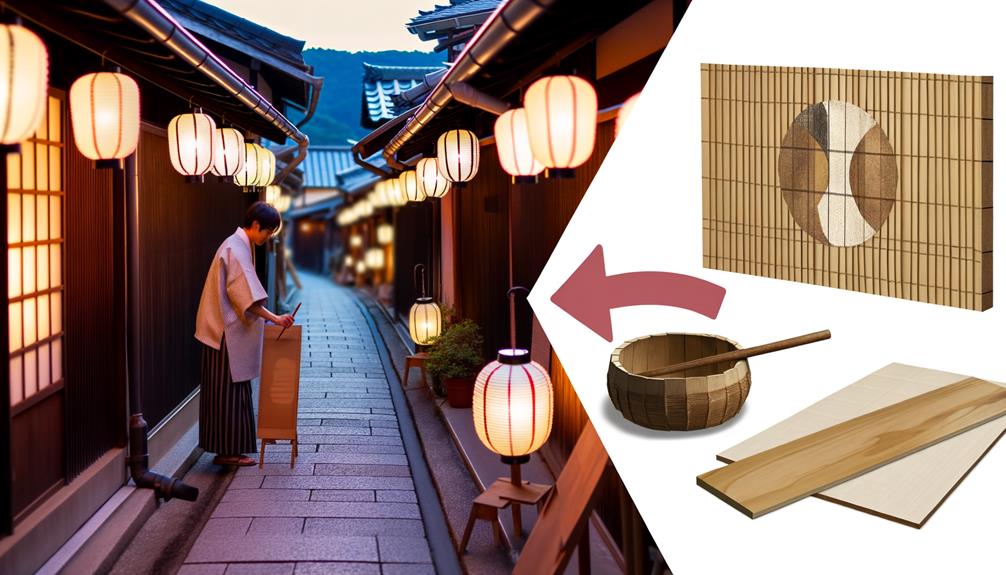
The origins of Kanban can be traced back to the early 1940s in Japan, where it was developed by Taiichi Ohno as a scheduling system for lean manufacturing at Toyota. Ohno aimed to improve efficiency by aligning production with actual demand, thereby reducing waste.
The term 'Kanban' translates to 'signboard' or 'visual card' in Japanese, reflecting its method of using visual cues to signal the need for inventory replenishment. Influenced by supermarket shelf-stocking methods, Ohno implemented a pull system that allowed workers to signal when new materials were needed.
This innovative approach enabled Toyota to achieve just-in-time production, enhancing operational efficiency and responsiveness to a great extent. Over time, Kanban evolved into a versatile tool applicable across various industries.
Key Principles
The key principles of Kanban center around visual workflow management and the commitment to continuous process improvement.
By making workflow visible through a Kanban board, teams can better understand and manage their tasks.
This visual approach, coupled with a focus on incremental improvements, fosters an environment of sustained efficiency and adaptability.
Visual Workflow Management
Visual workflow management in Kanban is founded on key principles that enhance transparency, efficiency, and collaboration within teams.
Central to this approach is the use of visual signals, such as cards and boards, to represent work items and their statuses. This visual representation allows team members to quickly grasp the current state of tasks, identify bottlenecks, and assess progress at a glance.
By limiting work in progress (WIP), Kanban ensures that teams focus on completing tasks before starting new ones, thereby maintaining a steady workflow.
Additionally, setting explicit policies and continuously visualizing process steps foster a shared understanding and accountability among team members, leading to more synchronized and effective project execution.
Continuous Process Improvement
Continuous process improvement in Kanban revolves around the principles of regular reflection, incremental changes, and a commitment to iterative enhancements. These principles foster a culture where teams continuously assess their workflow for potential improvements.
Regular reflection, often achieved through retrospectives, enables a deep understanding of what is working and what is not. Incremental changes ensure that adjustments are manageable and sustainable, avoiding the disruption of sweeping transformations. The commitment to iterative enhancements emphasizes that improvement is a constant journey rather than a destination.
Visual Cues
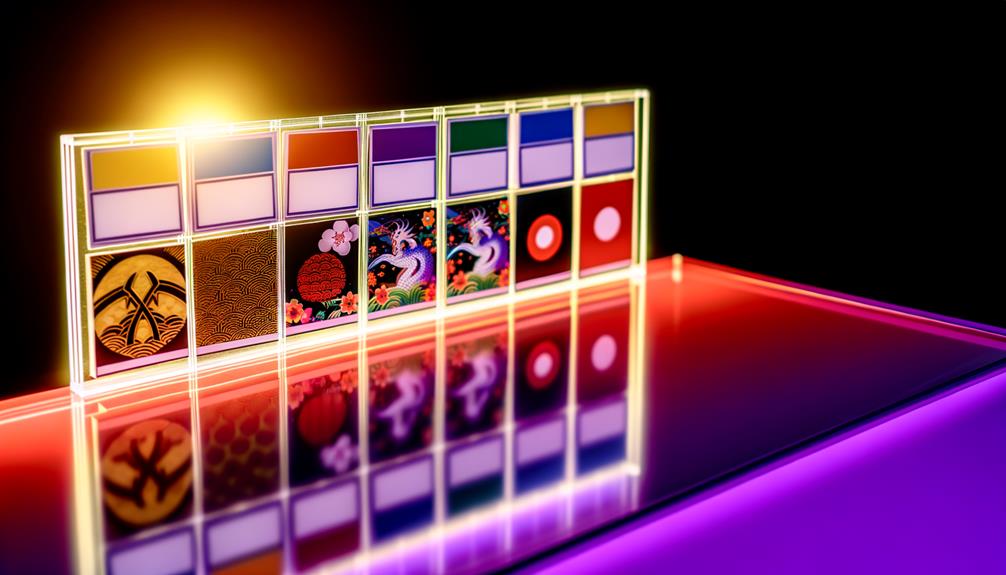
Visual cues play a pivotal role in the Kanban methodology by providing immediate and clear insights into project status. Color-coded task cards, workflow status indicators, and progress tracking boards are essential components that enhance visibility and streamline operations.
These tools not only facilitate communication but also enable teams to swiftly identify bottlenecks and areas requiring attention.
Color-Coded Task Cards
How can color-coded task cards enhance the efficiency and clarity of a Kanban system?
Color-coded task cards act as immediate visual cues, allowing team members to quickly identify the status, priority, and type of tasks at a glance. This method streamlines communication and reduces the time spent deciphering information, thereby improving overall workflow efficiency.
- Priority Identification: Easily distinguish high-priority tasks from lower-priority ones.
- Task Categorization: Group similar tasks together for better organization.
- Status Visibility: Instantly see which tasks are in progress or awaiting action.
- Role Assignment: Identify tasks assigned to specific team members or departments.
- Deadline Awareness: Highlight tasks with approaching deadlines, ensuring timely completion.
Thus, color-coded task cards significantly contribute to a more organized and efficient Kanban system.
Workflow Status Indicators
Effective workflow status indicators serve as vital visual cues that provide immediate insight into the progress and state of various tasks within a Kanban system. These indicators often include symbols, colors, and other visual elements that represent specific stages in the workflow, such as 'To Do,' 'In Progress,' and 'Completed.'
By leveraging these visual cues, teams can quickly assess the status of tasks, identify potential bottlenecks, and make informed decisions to maintain efficiency. The clarity provided by workflow status indicators also aids in fostering transparent communication among team members, ensuring everyone remains aligned with the project's goals.
Ultimately, these visual elements are essential for enhancing both individual and collective productivity within a Kanban framework.
Progress Tracking Boards
Building on the importance of workflow status indicators, progress tracking boards serve as the central framework for organizing and visualizing these cues within a Kanban system. These boards provide a visual representation of tasks at various stages, facilitating efficient workflow management and enhanced team collaboration.
The core components of an effective progress tracking board include:
- Columns: Represent different stages of the workflow, such as 'To Do', 'In Progress', and 'Done'.
- Cards: Visual elements that signify individual tasks or work items.
- WIP Limits: Constraints on the number of tasks in a specific stage to avoid overloading.
- Swimlanes: Horizontal divisions to categorize tasks by type or priority.
- Color Coding: Differentiates tasks by status, urgency, or department.
These elements collectively ensure a streamlined and transparent process.
Implementation Strategies
Implementing a Kanban system requires a clear understanding of its core principles and a structured approach to secure successful adoption. Begin by defining workflow stages, visualized on a Kanban board, to reflect the process from inception to completion.
Limit work in progress (WIP) to prevent bottlenecks and maintain steady task flow. Engage team members in regular reviews to identify inefficiencies and implement incremental improvements. Provide adequate training to foster a culture of transparency and continuous improvement.
Utilize metrics like cycle time and lead time to monitor performance and guide decision-making. Finally, ensure management support to align the Kanban system with organizational goals, facilitating a seamless integration into existing processes.
Benefits of Kanban
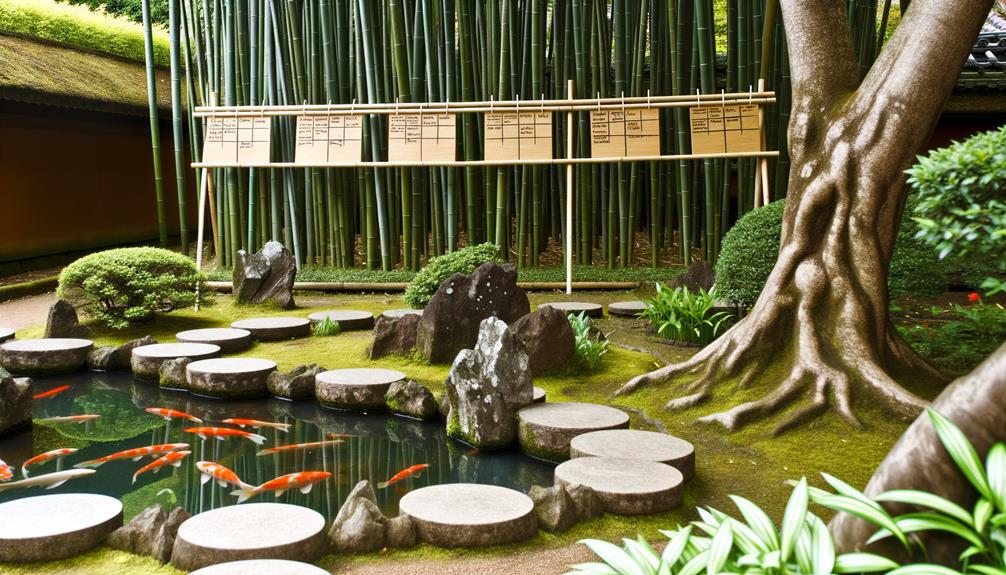
The Kanban methodology offers a range of benefits that enhance workflow efficiency, promote transparency, and support continuous improvement within organizations. By visualizing work processes and limiting work in progress, Kanban facilitates better task management and operational productivity.
Notable advantages include:
- Improved Workflow Efficiency: Streamlines processes by identifying bottlenecks and optimizing resource allocation.
- Enhanced Flexibility: Easily adaptable to changing priorities and customer requirements.
- Increased Transparency: Visual boards provide clear visibility of work status, fostering accountability.
- Continuous Improvement: Encourages incremental changes and iterative feedback for ongoing process enhancement.
- Better Collaboration: Promotes teamwork and communication through shared understanding of project stages.
These benefits collectively contribute to a more agile and responsive organizational environment.
Kanban Across Industries
Given the numerous benefits that Kanban offers, it is no surprise that this methodology has been successfully adopted across various industries to optimize workflows and enhance productivity. From manufacturing to software development, and even healthcare, Kanban's visual approach to managing tasks guarantees transparency and efficiency.
Industry | Application | Benefits |
---|---|---|
Manufacturing | Production line management | Reduces waste, improves quality |
Software Development | Task tracking and sprint planning | Enhances collaboration, speeds delivery |
Healthcare | Patient care coordination | Improves patient flow, reduces wait times |
Education | Curriculum planning | Streamlines lesson planning, increases engagement |
Marketing | Campaign management | Optimizes resource allocation, boosts ROI |
Conclusion
The etymology of the term 'kanban' in Japanese, meaning 'symbol' or 'box,' reflects its foundational role in visual management within diverse operational frameworks.
By adhering to key principles and employing strategic implementation, kanban facilitates efficiency and clarity.
Its benefits span numerous industries, underscoring its adaptability and universal applicability.
Further investigation into kanban's theoretical underpinnings and empirical successes could yield deeper insights, enriching its integration and potential advancements in various fields.