Hydraulic Check Valve Symbol Direction Flow: Explain!
In hydraulic systems, the check valve symbol is crucial for understanding flow direction. This symbol features an arrow indicating the direction fluid can flow freely, outlining the valve’s operational path.
Key components, like springs or balls, may be depicted to indicate specific types or functionalities. Incorrect interpretation can lead to system inefficiencies or damage.
Hence, it’s vital you identify the arrow’s orientation accurately to guarantee correct fluid dynamics.
Acknowledging these symbols allows for precise system analysis and troubleshooting, greatly impacting performance and reliability. With a deeper exploration, you’ll uncover subtleties that fine-tune your system’s efficiency and safety.
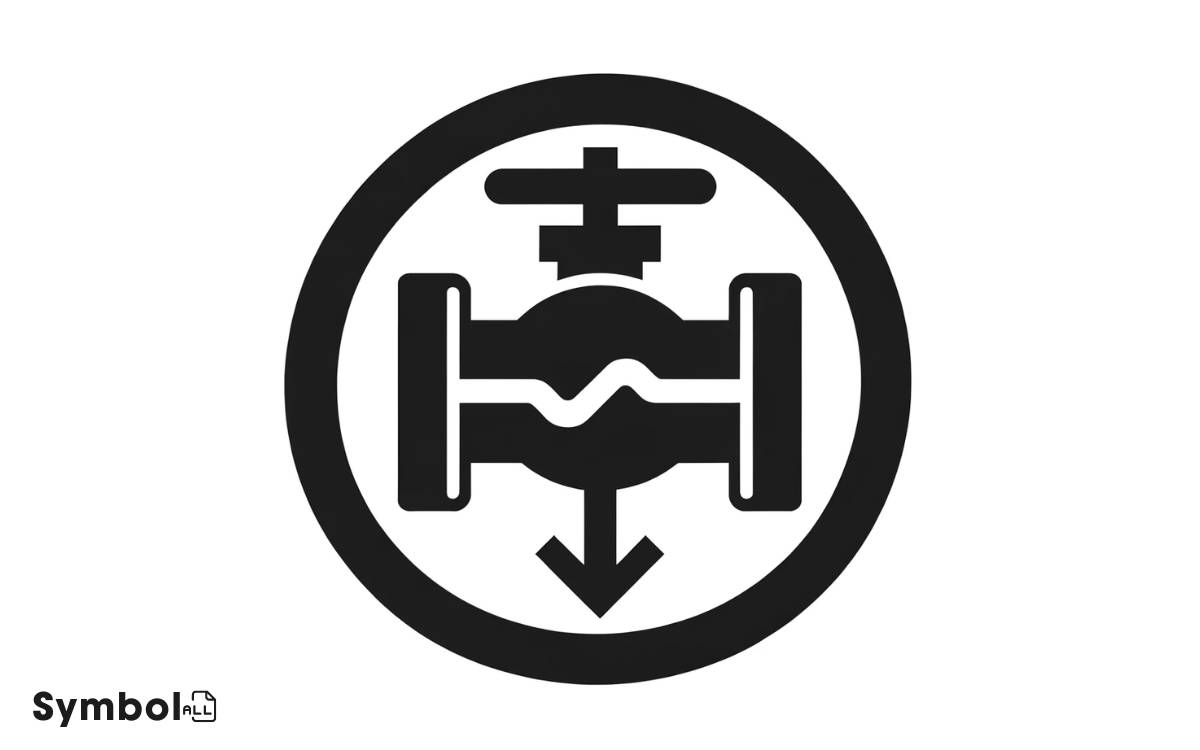
Key Takeaways
Understanding Hydraulic Symbols
To effectively interpret hydraulic circuits, you must first grasp the language of hydraulic symbols, which serves as the foundation for understanding complex fluid power systems.
Each symbol represents a component or function within the circuit, offering a concise visual representation that facilitates communication among engineers and technicians.
It’s important to familiarize yourself with these symbols, as they’re the building blocks for analyzing and troubleshooting hydraulic systems.
Recognizing the various symbols, such as pumps, motors, cylinders, and valves, allows you to decipher the flow paths, control mechanisms, and operational sequences within a circuit.
This knowledge not only enhances your analytical skills but also enables you to design and modify systems with precision.
Understanding hydraulic symbols is hence vital for anyone seeking to master fluid power technology.
The Role of Check Valves
Check valves play an important role in hydraulic systems by allowing fluid to flow in one direction while preventing backflow. These components are critical for maintaining the integrity and efficiency of a hydraulic circuit.
They guarantee that fluid doesn’t reverse its direction, which could potentially damage the system or diminish its performance.
Symbol Breakdown
Understanding the hydraulic check valve symbol and its flow direction indicators is essential for your system’s design and functionality.
You’ll interpret these symbols to verify that valves are properly implemented, facilitating smooth operation and preventing backflow.
Each element within the symbol provides insights into the valve’s mechanics and flow direction, guiding you in making informed decisions.
Valve Symbol Interpretation
Interpreting hydraulic check valve symbols necessitates a precise breakdown of each component within the symbol to effectively grasp its function and flow direction.
You’ll notice that the symbol typically consists of a single square block, indicating the valve body, with an internal arrow and sometimes a dashed line.
The arrow’s orientation is vital, as it represents the path that fluid can flow through the valve under normal conditions.
Understanding this orientation is key to grasping how the valve operates within a hydraulic system.
Additionally, variations like a spring symbol within the valve symbol denote a spring-loaded check valve, suggesting it requires a minimum pressure to open.
Flow Direction Indicators
To accurately determine the flow direction in a hydraulic check valve, it’s essential to closely examine the symbol’s internal arrow and any additional indicators.
This arrow, often simplistic yet highly significant, points towards the direction in which fluid is allowed to flow freely.
Surrounding the arrow, you might find other graphical elements that further specify conditions under which flow is permitted or restricted.
Understanding these symbols requires a keen eye for detail; for instance, a dashed line or a spring symbol adjacent to the arrow could imply conditional flow, based on pressure differentials across the valve.
Each nuance in the symbol provides critical information about how the valve operates under various hydraulic conditions, ensuring you’re equipped to make informed decisions about its application in your system.
Direction Flow Indication
In hydraulic systems, accurately identifying the flow direction through a check valve is crucial for peak performance. You’ll find that the symbol for a check valve incorporates specific directional cues.
These cues are essential for setting up the system correctly to guarantee that fluids flow in the intended direction, preventing backflow that could lead to system failure.
Symbol Feature | Indicates |
---|---|
Arrow | Flow direction |
Solid line | Valve body |
Dashed line | Optional paths |
T-shape | Blocked path |
Diagonal slash | Check mechanism |
Understanding these elements allows you to interpret how the valve functions within the hydraulic circuit and ensures that you’re aligning components in a manner that optimizes the system’s efficiency and reliability.
Reading Hydraulic Schematics
To accurately interpret hydraulic schematics, you must first grasp schematic symbols. Each symbol, including flow direction indicators and valve types, provides critical information about the system’s operation.
Mastering these elements allows for precise identification and analysis of hydraulic circuits.
Understanding Schematic Symbols
Mastering the interpretation of hydraulic schematic symbols is essential for diagnosing and troubleshooting system operations effectively.
Each symbol represents a specific component or function within the hydraulic system, allowing you to understand the flow and interactions without physically inspecting the machinery.
Symbol | Component | Functionality |
---|---|---|
⬜️➡️⬜️ | Hydraulic Pump | Generates fluid flow |
⬛️ | Fixed Displacement Motor | Converts hydraulic energy to mechanical |
⚫️➡️⚪️ | Directional Valve | Controls flow direction |
⬆️⬇️ | Pressure Relief Valve | Limits maximum system pressure |
🔄 | Reservoir | Stores hydraulic fluid |
Understanding these symbols allows for a precise reading of hydraulic schematics, leading to accurate diagnostics and efficient system management, devoid of guesswork.
Flow Direction Indicators
Understanding flow direction indicators within hydraulic schematics is crucial for accurately evaluating system functionality.
These indicators help you interpret how fluid moves through the components and which path it takes under various conditions.
Here’s what to look for:
- Arrow symbols: Indicate the primary direction of flow.
- Solid lines: Represent the main flow path.
- Dotted lines: Show secondary or alternative flow paths.
- Check valve symbols: Highlight one-way flow restrictions.
- T-junctions: Suggest flow splitting or combining points.
Grasping these elements allows for a deeper understanding of hydraulic system operations. It’s not just about recognizing the symbols but understanding their implications on system behavior.
This foundational knowledge is essential for troubleshooting and optimizing hydraulic systems, ensuring they operate as intended without unnecessary complications.
Valve Identification Techniques
Decoding valve symbols on hydraulic schematics requires a sharp eye and a solid understanding of technical nuances, enabling you to accurately interpret system configurations.
Recognizing specific symbols that represent various valve types, their flow directions, and functionalities is crucial.
Here’s a brief guide to help you navigate through these technical symbols:
Symbol | Valve Type | Functionality |
---|---|---|
→( ) | Check Valve | Allows flow in one direction, blocks in the opposite |
T | Tee Valve | Diverts flow into two directions |
⊥ | Shut-off Valve | Opens/closes the flow path |
↺ | Throttle Valve | Adjusts the flow rate |
Comprehending these symbols enhances your ability to analyze hydraulic circuits effectively. Each symbol contains crucial information about the valve’s role within the system, offering insights into the circuit’s design and operational logic.
Symbol Variations
Hydraulic check valve symbols can vary greatly, often reflecting the specific function or design characteristics of the valve.
You’ll notice that symbols often provide insight into how a valve operates within a hydraulic system, guiding your understanding and application of these components.
Specifically, variations in symbols can indicate:
- Direction of flow: Shows the allowed direction of fluid through the valve.
- Cracking pressure: A detail that may be represented to specify the minimum upstream pressure required to open the valve.
- Spring-loaded or not: Differentiates symbols to indicate the presence of a spring mechanism.
- Ball or poppet design: Symbol modifications can suggest the type of mechanism used inside the valve.
- Bi-directional flow capabilities: Some symbols might hint at the ability for fluid to flow in both directions under certain conditions.
Understanding these variations is essential for accurate system design and troubleshooting.
Common Misinterpretations
Why do some professionals misinterpret the subtle nuances in hydraulic check valve symbols, leading to errors in system design or maintenance? It’s often a matter of overlooking the details that distinguish one type of check valve from another.
Here’s a quick guide to common misinterpretations:
Symbol Feature | Common Interpretation | Correct Interpretation |
---|---|---|
Arrow Direction | Flow direction only | Flow allowance direction |
Dashed Line | Optional component | Pilot operated control |
Spring Symbol | Always present | Optional, for spring-loaded |
Circle | Generic component | Specific check valve type |
Diagonal Line | Flow restriction | Check feature presence |
Understanding these symbols correctly ensures precise reading and implementation of hydraulic schematics, minimizing errors in system design and maintenance.
Recognizing the significance of each detail in these symbols is essential for precision and efficiency in hydraulic systems operations.
Practical Application Tips
To effectively implement hydraulic check valves in your systems, it’s crucial to apply the correct interpretation of their symbols with precision.
Understanding these symbols allows for accurate installation and operation, ensuring your hydraulic systems function at their best.
Here are key points to keep in mind:
- Confirm the valve’s flow direction matches the system’s requirements.
- Verify compatibility with the hydraulic fluid used.
- Use proper fittings to avoid leaks or pressure drops.
- Install in accessible locations for easy inspection.
- Be mindful of the valve’s pressure rating to prevent failures.
Adhering to these tips when integrating hydraulic check valves into your setup will enhance system reliability and efficiency.
Remember, precision in application translates to peak performance and longevity of your hydraulic systems.
Maintenance and Troubleshooting
To guarantee your hydraulic check valves function at their best, you’ll need to conduct regular inspections. Identifying common issues requires a sharp eye and a solid understanding of potential solutions.
This section outlines effective strategies for maintenance and troubleshooting, focusing on practical steps for addressing valve malfunctions.
Regular Inspection Tips
How frequently do you inspect your hydraulic check valves for peak performance and to avoid system failures?
Regular inspection is crucial for maintaining the integrity and functionality of your hydraulic systems.
Here’s a precise guide to what you should focus on during inspections:
- Visual Examination: Look for any signs of wear, damage, or leaks.
- Pressure Testing: Guarantee the valve maintains the correct opening and closing pressures.
- Flow Rate Checks: Confirm that the flow rate matches the system’s specifications.
- Seal Integrity: Inspect seals for degradation or damage.
- Operational Testing: Verify the valve operates smoothly without any delays or hitches.
Common Issues Solutions
Several common issues can arise with hydraulic check valves, requiring specific maintenance strategies and troubleshooting techniques for best performance.
You’ll find that addressing these problems promptly guarantees your system operates efficiently and reliably.
Issue | Symptom | Solution |
---|---|---|
Blockage | Reduced flow rate | Clean or replace valve |
Wear | Leakage, erratic operation | Inspect and replace worn components |
Incorrect Installation | No flow or reverse flow | Reinstall according to manufacturer’s guidelines |
Spring Failure | Continuous flow in one direction | Replace the spring |
Pressure Surges | System shocks, noise | Install surge protectors or dampeners |
Diagnosing and solving these issues requires a methodical approach. Regularly inspect your hydraulic check valves, adhering to the manufacturer’s maintenance schedule, and replace parts with high-quality substitutes to ensure longevity and peak performance.
Advanced Symbols Overview
As you delve deeper into hydraulic systems, grasping the intricacies of advanced symbols, especially for check valves, becomes essential for precise system analysis and design.
Advanced symbols include more than just basic flow directions; they embody the valve’s operational characteristics and its response under different conditions.
Understanding these symbols enables you to:
- Identify pilot-operated check valves
- Distinguish between single and double-acting check valves
- Recognize symbols indicating adjustable flow rates
- Understand symbols for integrated bypass circuits
- Decode symbols representing pressure-dependent closures
Each symbol provides critical information about the valve’s function, ensuring you don’t just see a component, but understand its role and limitations within the hydraulic system. This level of detail is vital for designing efficient and reliable systems.
Case Studies
Building on your understanding of advanced symbols, let’s explore case studies to see these components in action within hydraulic systems.
In one instance, a hydraulic system designed for a manufacturing press utilized a series of check valves to guarantee unidirectional flow, enhancing operational reliability.
The precise symbols provided in the schematics allowed engineers to pinpoint inefficiencies in the system, particularly where fluid dynamics were causing delays in machinery response times.
Another case involved an agricultural machinery setup, where check valves played an essential role in controlling the flow to hydraulic cylinders, ensuring smooth and consistent operation across varying loads.
By analyzing these practical applications, you’ll grasp how accurately interpreting these symbols translates to improved system designs and troubleshooting capabilities.
Future Trends in Hydraulic Design
The evolution of hydraulic design is poised to incorporate advanced technologies, optimizing system efficiency and performance.
You’ll notice a significant shift towards:
- Integration of IoT devices for real-time monitoring and diagnostics.
- Application of AI and machine learning to predict system failures and optimize performance.
- Use of advanced materials to reduce weight and improve durability.
- Adoption of 3D printing technologies for custom components, reducing lead times and costs.
- Increased focus on environmental sustainability, with designs that minimize energy consumption and hydraulic fluid leakage.
These advancements promise to revolutionize hydraulic systems, making them smarter, more efficient, and more reliable.
You’re witnessing a pivotal moment in hydraulic design, where innovation meets practical application, ensuring systems aren’t only powerful but also intelligently responsive to their operational environment.
Conclusion
In wrapping up, it’s essential to grasp that nearly 75% of hydraulic system failures stem from incorrect valve implementation or maintenance.
You’ve now got the tools to decipher hydraulic check valve symbols and understand their flow direction, a fundamental step in troubleshooting and enhancing system efficiency.
Remember, accurate reading of hydraulic schematics not only prevents downtime but also paves the way for future innovations in hydraulic design.
Stay ahead by keeping these insights at your fingertips.