Check Valve Flow Direction Symbol: Identify it!
To guarantee your system functions efficiently and safely, you must accurately identify the check valve flow direction symbol.
This symbol typically consists of an arrow indicating the direction fluid should flow, preventing backflow and system failures. Understanding this arrow’s orientation is vital for correct installation and maintenance.
Additionally, inlet and outlet markings help orient the valve properly within the system. Diagonal line(s) or a circle/semi-circle shape can further denote the check mechanism type and valve body, respectively.
Recognizing these symbols aids in optimizing system performance and safety. Grasping the full significance of these symbols enhances your understanding of system design and functionality.
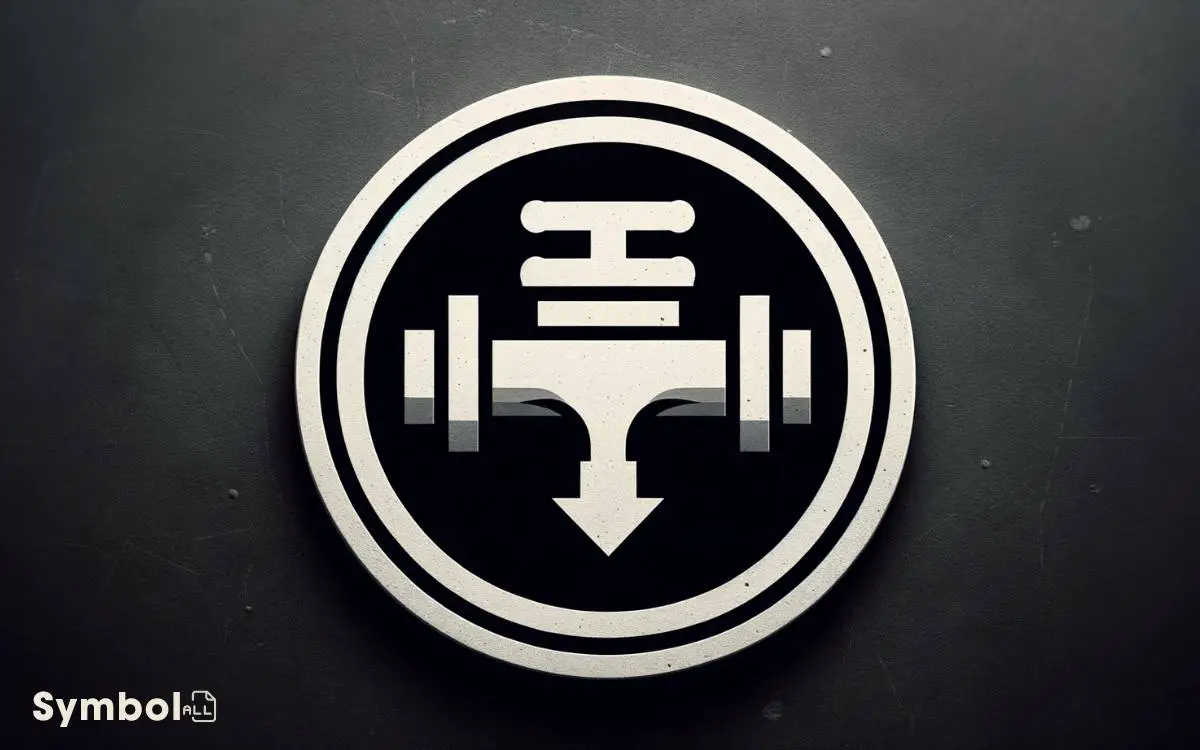
Key Takeaways
Understanding Check Valves
Check valves, essential components in fluid control systems, allow fluid to flow in one direction while preventing backflow. You’ll find them integral in preventing the reverse movement of liquids or gases, which could compromise system integrity or function.
Their operation is based on differential pressure; when upstream pressure exceeds downstream, the valve opens. Conversely, it closes when downstream pressure attempts to reverse, effectively acting as a non-return barrier.
Understanding the mechanics involves recognizing types like swing, lift, and diaphragm check valves, each designed for specific flow characteristics and installation environments.
It’s important to select the appropriate type based on fluid properties, pressure conditions, and the required response time to changes in flow direction to guarantee performance and longevity of your system components.
Significance of Flow Direction
Correct installation and operation of a check valve hinge heavily depend on understanding the importance of flow direction in your system.
You must acknowledge that improper installation can result in severe system failures, including backflow, which can jeopardize the integrity of the entire system.
Below is a table that outlines crucial aspects related to flow direction:
Aspect | Importance | Consequence of Lack of Awareness |
---|---|---|
Backflow Prevention | Guarantees fluid flows in the intended direction | System contamination, potential failures |
Pressure Differential | Aids valve functionality | Ineffective operation, increased wear |
System Efficiency | Maximizes flow and reduces energy consumption | Higher operational costs, decreased lifespan |
Understanding these aspects ensures that your check valve operates effectively, safeguarding your system’s integrity and optimizing performance.
Identifying the Flow Symbol
In order to guarantee the check valve functions correctly, you must accurately identify the flow direction symbol. This involves grasping symbol interpretation essentials, which are crucial for both novice and seasoned engineers.
Proper installation guidance hinges on this knowledge, preventing potential system failures.
Symbol Interpretation Essentials
Understanding the symbol that signifies flow direction in a check valve is essential for accurate system design and maintenance. This symbol, often overlooked, plays a pivotal role in ensuring the correct operation of fluid systems.
Here are key elements to identify and interpret this significant symbol:
- Arrow Indicator: A clear arrow marks the intended flow direction, guiding fluid movement through the valve.
- Inlet and Outlet Markings: Identifiable markings distinguish between the inlet (entry point) and outlet (exit point), critical for proper valve orientation.
- Color Coding: In some schematics, color coding aids in distinguishing flow direction, with specific hues representing flow paths.
Correct Installation Guidance
Identifying the flow direction symbol is a vital step in ensuring your check valve is installed properly for peak system performance. This symbol, often a simple arrow, indicates the correct orientation of the valve in the piping system.
Misinterpretation or oversight can lead to reverse installation, severely impairing the valve’s function and potentially causing system failure. You’ll find the symbol engraved or stamped on the valve body, pointing towards the direction of fluid flow.
It’s imperative you cross-reference this with your system’s flow direction before installation. Ensuring alignment with the flow direction not only optimizes the valve’s efficiency but also prolongs its service life, minimizing the risk of backflow and the associated damages.
Paying close attention to this detail is essential for system integrity.
Installation Guidelines
As you proceed with the installation of check valves, it’s vital to adhere to correct orientation tips to guarantee peak functionality and prevent backflow.
Understanding flow arrows on the valve body guides you in aligning the valve in the correct direction, enhancing system efficiency.
Additionally, factor in maintenance access considerations, enabling easy inspection and repair without compromising system integrity.
Correct Orientation Tips
To guarantee top performance and prevent reverse flow, it’s crucial to install the check valve with the correct orientation, following the manufacturer’s guidelines. Achieving peak functionality entails adhering to precise installation protocols.
Here are three critical considerations:
- Vertical vs. Horizontal Placement: Ascertain the valve’s design specification for vertical or horizontal installation. Misalignment can lead to malfunction or degraded performance.
- Flow Direction Markings: Identify and align the valve according to the flow direction indicated by the manufacturer. Incorrect orientation could result in backflow and potential system failure.
- Pressure Differential Requirements: Ensure the operating pressure is within the valve’s specified range. Insufficient pressure differential can prevent the valve from opening, while excessive pressure may cause premature wear or damage.
Adhering to these guidelines guarantees the check valve functions as intended, safeguarding your system against reverse flow and related complications.
Understanding Flow Arrows
Building on the importance of correct orientation, understanding flow arrows plays a key role in guaranteeing your check valve’s best installation and operation.
Flow arrows, etched on the valve body, indicate the direction fluid is meant to travel through the valve. It’s important you install the check valve so that the medium flows in alignment with these arrows. Deviating from this directive can lead to backflow, valve damage, or system failure.
Precise adherence to the indicated flow direction ensures the valve operates efficiently, preventing reverse flow and potential contamination. Additionally, correct installation as per the flow arrows optimizes the valve’s lifecycle, minimizing wear and tear.
Essentially, these arrows aren’t mere suggestions but critical guides to secure performance and longevity of your check valve system.
Maintenance Access Considerations
In planning for check valve installation, it’s important to consider maintenance access to guarantee effective future servicing and inspections.
Ensuring unobstructed access not only facilitates routine maintenance but also extends the valve’s operational lifespan.
Consider the following:
- Clearance: Make sure there’s ample space around the check valve for tools and equipment. This space is vital for performing diagnostics, repairs, or replacements without hindrance.
- Accessibility: Place the valve in a location that’s easily reachable. Avoid cramped or elevated spaces where accessing the valve requires additional safety measures or equipment.
- Service Panels: If possible, incorporate removable service panels in the system design. These panels allow for direct access to the check valve without the need to dismantle adjacent piping or components, reducing downtime significantly during maintenance activities.
Common Types of Check Valves
Several common types of check valves, each with unique characteristics, regulate fluid flow direction in various systems. You’ll find these valves indispensable in preventing backflow and ensuring that your systems operate efficiently and safely.
Below is a concise overview of these valves:
Type | Functionality | Applications |
---|---|---|
Swing | Uses a swinging disc to block flow | Water, sewage systems |
Ball | Employs a spherical ball to seal | Fuel, air systems |
Diaphragm | Utilizes a flexible diaphragm | Chemical, food industries |
Lift | Lifts a disc or cone against gravity | High-pressure applications |
Dual Plate | Features two spring-loaded plates | HVAC, industrial processes |
Each type’s design and operational mechanism cater to specific needs, ensuring top performance in controlling fluid direction across diverse environments.
Reading Symbols Correctly
Understanding check valve flow direction symbols is vital for ensuring the best performance and safety of your fluid control systems. These symbols provide critical information on how the valve operates within the system, guiding you in installing and maintaining it correctly.
Here’s what you need to look for:
- Arrow Indication: The arrow symbolizes the flow direction through the valve, essential for proper installation.
- Diagonal Line(s): Represents the check mechanism, indicating whether it’s a swing, lift, or other type of check valve.
- Circle or Semi-circle Shape: Denotes the valve body, with variations suggesting specific features or functions.
Recognize these symbols to ensure you’re not only installing the valve correctly but also utilizing its design for the best system performance.
Mistakes to Avoid
You must recognize that incorrect installation of a check valve can lead to catastrophic system failures, emphasizing the criticality of understanding flow direction symbols accurately.
Misinterpreting these symbols not only jeopardizes system integrity but also escalates maintenance costs.
Hence, ensuring proper orientation during installation is paramount to prevent operational inefficiencies and potential hazards.
Incorrect Installation Impact
Installing a check valve in the wrong direction severely compromises its efficiency and can lead to system failure.
This erroneous installation impacts the system’s functionality in several critical ways:
- Backflow Prevention Failure: The primary function of a check valve is to prevent backflow. Incorrect installation reverses this, allowing contaminated fluids to mix with the clean supply.
- Pressure Surge Risks: When installed backwards, the valve won’t mitigate pressure surges. This oversight can result in a phenomenon known as water hammer, potentially damaging the piping system and connected machinery.
- Increased Maintenance Costs: Operating in an unintended manner accelerates wear and tear on the valve, necessitating frequent replacements and repairs, thereby elevating maintenance expenses.
Understanding these impacts underscores the importance of meticulous adherence to installation guidelines, ensuring system integrity and operational efficiency.
Misreading Symbols Consequences
Recognizing the severe impacts of incorrect installation, it’s also imperative to avoid misreading check valve flow direction symbols to guarantee system reliability.
Misinterpreting these critical symbols can lead to backflow, where media flows opposite the intended direction, potentially causing system failure or damage to components.
This misstep not only jeopardizes the integrity of the system but also escalates maintenance costs and downtime.
Additionally, in applications involving hazardous materials, the consequences can extend to safety hazards, posing risks to both personnel and the environment.
Hence, a meticulous examination of these symbols during installation isn’t just recommended, it’s essential.
Familiarizing oneself with the standard symbols and their meanings, along with regular verification, minimizes the risk of such costly errors, ensuring both operational efficiency and safety.
Proper Orientation Importance
Ensuring the correct orientation of check valves is essential to prevent operational failures and maintain system integrity. Incorrect installation can lead to several complications that adversely affect the performance and reliability of your fluid system.
Here are key mistakes to avoid:
- Backflow Prevention Failure: Installing a check valve backwards can render the backflow prevention mechanism ineffective, leading to potential system contamination or damage.
- Pressure Surges: Incorrect orientation may cause sudden pressure surges, known as water hammer, risking damage to the valve and connected equipment.
- Reduced Lifespan: A valve installed in the wrong direction can experience premature wear and tear, resulting in a reduced operational lifespan and increased maintenance costs.
Understanding these risks emphasizes the importance of adhering to proper valve orientation guidelines, ensuring system safety and efficiency.
Symbol Variations Across Systems
Different systems utilize varying symbols to represent check valve flow direction, reflecting their unique operational requirements and standards.
You’ll find that, in hydraulic systems, symbols often include detailed representations of the valve’s internal mechanism, highlighting the directional flow control features.
Conversely, in pneumatic systems, the symbols might be simplified, focusing on the directionality rather than the specific internal configurations. This variation guarantees that professionals can quickly identify the check valve’s function within the system’s context.
Additionally, water and wastewater management systems adopt a symbol set that emphasizes backflow prevention capabilities, vital for maintaining system integrity.
Understanding these symbol variations is essential for you, as it facilitates accurate interpretation and application in diverse engineering and technical environments, ensuring system compatibility and functional efficacy.
Maintenance and Inspection Tips
After mastering the variations in check valve flow direction symbols across systems, you’ll find that regular maintenance and inspection are crucial to their peak performance.
To guarantee their best functionality and to prevent potential system failures, consider these critical steps:
- Visual Inspection: Routinely examine the valve for signs of wear or damage. Look for cracks, corrosion, or any deformities on the valve body and sealing surfaces.
- Operational Testing: Periodically test the valve’s opening and closing response under various flow conditions. This ensures the valve responds appropriately to changes in system pressure.
- Seal Integrity Checks: Verify the integrity of the seals and gaskets. Even minor leaks can indicate compromised sealing elements, necessitating immediate replacement to maintain system efficiency and safety.
Following these guidelines will extend the lifespan of your check valves and maintain system reliability.
Advanced Applications
Exploring advanced applications reveals how check valves play pivotal roles in complex fluid dynamics systems, requiring precision engineering to optimize performance.
In high-pressure scenarios, such as in hydraulic systems or power generation plants, the integrity and responsiveness of a check valve are paramount.
You’ll find that the materials selected, alongside the valve’s design, directly impact its ability to withstand rapid pressure fluctuations without succumbing to wear or failure.
Additionally, in systems where fluid contamination poses significant risks, like in pharmaceutical manufacturing, check valves must offer exceptional sealing capabilities.
Here, your understanding of the valve’s flow direction symbol becomes essential it guides installation, ensuring the valve functions correctly, preventing backward flow, and safeguarding the system’s integrity.
Precision in selecting and installing check valves is non-negotiable for advanced applications, emphasizing the need for rigorous attention to detail.
Conclusion
In wrapping up, recognizing the right flow direction and deciphering the dedicated symbols for check valves are essential components for correct installation. Adhering to accurate analytical assessments aids in avoiding adverse application anomalies.
Meticulously maintaining and monitoring your mechanisms guarantees enduring efficiency. Famously, familiarizing yourself with the variety of valve varieties and vigilantly verifying their symbols across systems greatly safeguards system stability.
So, steadfastly study symbols, sidestep slip-ups, and secure system success.